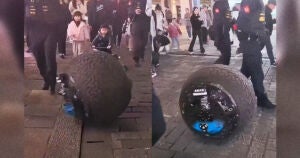
Imperial Police
In Eastern China, police are now patrolling the streets with a rolling robot that can chase down suspects — and, they say, beat them in a fight.
As the South China Morning Post reports, cops in the city of Wenzhou in Zhejiang province have lately been flanked by the spherical robot that looks a bit like a militarized version of the cutesy BB-8 robot in "Star Wars."
Named the "Rotunbot" or "RT-G" for short, this spherical robot was created by researchers at Zhejiang University on behalf of a Shenzen-based outfit called Logon Technology. It reportedly weighs about 275 pounds and travels up to 22 miles-per-hour — and according to Wang You, an associate professor who worked on it, only takes a few seconds to reach that speed.
"This robot can cope with dangers such as falling or being beaten," Wang told SCMP, "and can perform tactical actions such as enemy identification, tracking, and capture after modular modification."
Equipped with net-guns, tear gas, and speakers, the robot is also reportedly pretty good at scaring off any would-be attackers.
"If you win the fight, you’ll end up in jail," the robot was heard saying in a recent fight simulation viewed by the SCMP. "If you lose the fight, you’ll end up in hospital."
Burning Rubber
While "Star Wars" aesthetics are very much present in RT-G's design, its autonomous operations are more akin to the 2010 sleeper horror hit "Rubber," which follows a sentient tire as it wreaks havoc across a desertscape.
Though there don't seem to have been any public demonstrations of the robot operating autonomously yet, a promotional video released by Logon ahead of RT-G's deployment in Wenzhou suggests it can navigate various types of situations by itself.
"Narrow terrain, extreme weather, dangerous work environments, violent conflicts and wars, all pose huge threats to human life and activities," reads a translation of the video on the r/Cyberpunk subreddit. "Thus an amphibious, intelligent robot emerged to replace humans in these style environments."
It's a far cry from the crappy police robots that have been repeatedly deployed and recalled by law enforcement in New York — and honestly, this one is a lot scarier.
More on cop-bots: Eric Adams Has Been Indicted, But His Crappy Subway Robot Will Be "Redeployed"
The post Chinese Police Deploy Rolling BB-8-STyle Robot to Patrol Streets, Chase Down Suspects appeared first on Futurism.
Read more:
Chinese Police Deploy Rolling BB-8-STyle Robot to Patrol Streets, Chase Down Suspects